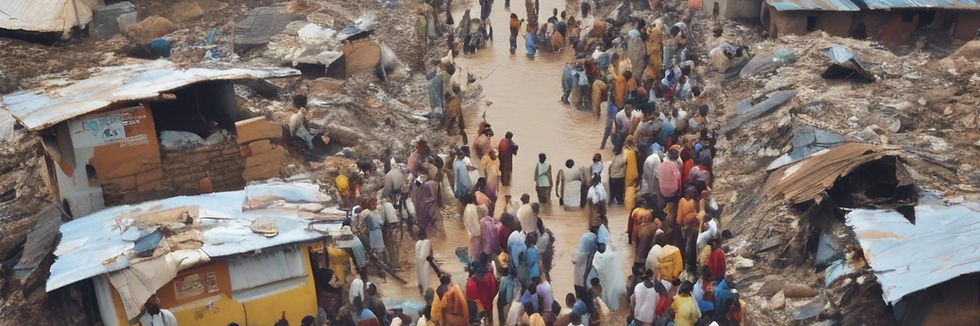
Warehouse Design X DMart
Reimagining Fulfillment Center Operations Through Human-Centered Design
A comprehensive redesign initiative that transformed warehouse operations by prioritizing both efficiency and worker wellbeing.
The Challenge
DMart's fulfillment center faced critical operational challenges: excessive picker travel time, frequent order errors, and ergonomic issues leading to worker strain. These inefficiencies created a ripple effect, impacting operational costs, worker satisfaction, and ultimately, customer experience. As Program Manager in the CEO's office, I was tasked with reimagining the entire fulfillment system.
My Role & Contribution
Leading this complex redesign project required balancing operational efficiency with human factors. My responsibilities included:
Strategic Design
-
Conducted in-depth analysis of order patterns and item placement
-
Applied information architecture principles to optimize picking routes
-
Developed adaptive zoning systems for inventory management
Technology Integration
-
Orchestrated integration of automation solutions
-
Implemented automated scanning and verification systems
-
Designed human-machine collaboration workflows
Human-Centered Implementation
-
Designed ergonomic workstations and clear movement pathways
-
Created comprehensive training programs for new systems
-
Established performance monitoring and feedback loops
Request Management System User Flow

The Solution
Our approach centered on three core design principles:
Efficiency Through Design
-
Strategic item placement based on order frequency
-
Optimized picking routes and workflows
-
Flexible zones adapting to inventory changes
Worker Wellbeing
-
Ergonomic workspace design
-
Structured break schedules
-
Clear safety protocols and pathways
Smart Automation
-
Robotic picking assistance
-
Conveyor systems integration
-
Automated verification processes
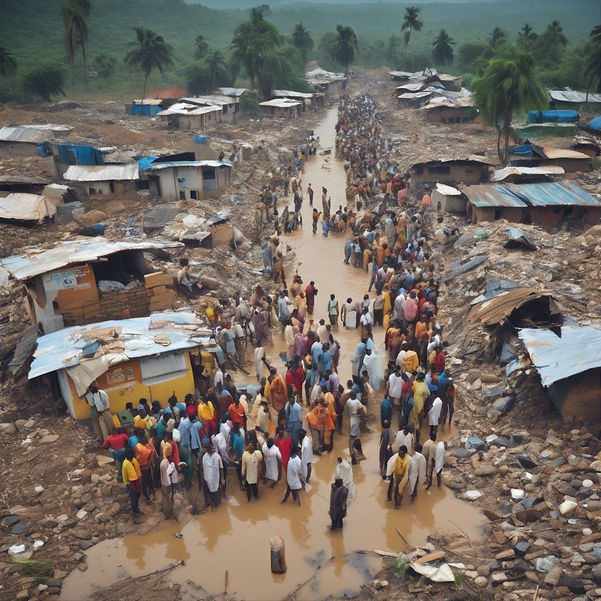
Impact & Outcomes
The redesign delivered measurable improvements across multiple dimensions:
Operational Excellence
-
20% increase in order packing speed over 4 months
-
1.5% reduction in damaged items monthly
-
0.5% decrease in missed items per basket
Worker Experience
-
Improved workplace satisfaction scores
-
Enhanced goal tracking and performance visibility
-
Better-structured break schedules
Business Value
-
Reduced operational costs
-
Improved customer satisfaction
-
Enhanced workforce retention
Key Learnings
This project reinforced crucial principles in design management:
Systems Thinking
Complex operational challenges require holistic solutions that consider all interconnected elements—from technology to human factors.
Human-Centered Design
Success in operational design comes from deeply understanding and addressing user needs, whether they're workers or end customers.
Iterative Implementation
Continuous monitoring and adjustment based on real-world feedback is essential for sustainable improvement.